Salon is an online magazine that focuses on politics and current affairs. Its stories often use strong wording and are left-leaning. They also tend to use untrusted sources.
In recent years, Salon has been criticized for its poor financial performance and imprudent management. It has never been profitable and has faced several rounds of layoffs. Contact I AM Salon now!
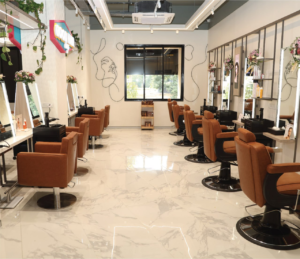
The Regis Salon is a chain of beauty salons that offers a wide variety of hair and nail services. Its stylists are well trained and use the latest techniques to create fashionable styles for clients. The Salon also carries a full line of hair products, including shampoos, conditioners, and styling tools. The company also offers seasonal promotions and discounts for customers.
The Salon is open Monday through Friday from 7:00 am to 8:00 pm, and Saturdays from 9:00 am to 5:00 pm. It is closed on Sundays and holidays. Customers can make an appointment online or by calling the Salon. The customer service department is available to help customers with questions or problems. The website provides contact information for each branch, as well as directions to the nearest location.
In addition to hairstyling, the Salon also offers manicures and pedicures. Some locations offer gel manicures and pedicures, which are more durable and last longer than traditional polish. The salons are also equipped to perform color treatments, and many offer hair straightening services as well.
Salon Regis offers a range of hair care and styling services for men and women. Some of their most popular offerings include haircuts, blow drys, color services, and highlights. They are also known for their friendly staff and affordable prices.
Regis has over 5,563 salons worldwide, and is a leader in the beauty industry. The company has a strong focus on its franchisees and a commitment to customer satisfaction. They are constantly training their stylists and providing them with the best products and tools to meet their client’s needs.
The company has a long history of growth, and has acquired a number of brands and businesses. In recent years, it has focused on expanding into new markets. For example, it has purchased a number of salons in India. Its expansion strategy has been a success, and it has seen significant profits as a result.
Another area of the business that is growing is its salon education business. The company offers various courses in a range of hair and nail services, and is certified to accept Title IV student financial assistance. This makes it a great choice for those looking to get a quality education while still working in their local community.
The Regis Salon app is a convenient way to make appointments, track rewards, and receive special offers. The app is free to download and available on both iOS and Android devices. It allows you to view upcoming appointments and reschedule them on the go. It also lets you track loyalty points and redeem them when needed. If you are a frequent client, you can even schedule your next appointment right from the app! This makes it easy to keep up with your beauty routine.
Salon Maison de Joelle
Maison de Joelle is a beauty salon that offers a wide variety of services for clients looking to enhance their natural looks. Its elegant ambiance and commitment to excellence make it a popular choice for those who want to look their best. Its highly trained staff and top-notch equipment ensure a relaxing experience for all. The Salon’s visually striking gold and white decor creates a luxurious and welcoming atmosphere. Guests appreciate the professionalism of its staff, with many raving about how beautiful they look after a visit.
The Salon specializes in nail art and hair styling. It also provides a variety of spa treatments and massages. The prices are competitive and the staff is friendly. The Salon also offers a range of products, including L’Oreal Professionnel and Orly Nail Care. The Salon is located in the heart of Dubai and is easily accessible by public transportation.
With nine branches in the Middle East, Maison de Joelle is a leading beauty house that has launched a series of successful projects. It is a true reflection of the sophisticated taste of its owner, Joelle Mardinian, a talented Make-up Artist and beauty expert who gained her qualifications in the UK. It is featured weekly on MBC1 in a reality TV show called “Joelle,” where the Salon’s clients undergo transformations incorporating all of the services offered, including complete makeovers.
The company has a strong presence in the Saudi market, where it has established a network of salons in the major cities. Its customer support team responds to all queries within 24 hours and aims to provide the most personalized service possible. The website is easy to navigate and the team is available via phone, email, and live chat.
Salon Atelier
If you have ever dreamed of owning your own Salon, it may be the right time to make it a reality. However, if you are new to the beauty industry, it is important to understand the different types of salon services before launching your business. Hair salons are the most prevalent type of Salon, offering a wide variety of treatments to meet customer needs. Whether you want to style or color your hair, or want to try out a new haircut, there is a salon for you.
The Salon also offers a wide range of styling and smoothing services, including ammonia-free coloring and bespoke cuts. It also has a retail boutique that sells products by Ouidad, TIGI, IGK, Truss, and Leaf and Flower. Its hair care professionals are trained in the Ouidad RiCi cutting technique and are certified to offer their clients the best advice on managing curly hair.
Nikki Fallon, a stylist at the Salon Atelier, has been in the industry for eight years and loves her job more than ever before. She says it never feels like work and that every client leaves the Salon feeling beautiful. She loves to keep up with the latest styles and techniques, but always maintains her own flair. She believes that the greatest joy in her career is making clients happy.
There are many other types of salons that offer a wide variety of services, such as nail and spa salons, makeup salons, or hybrids. These salons offer multiple services in one location and are popular among customers looking for a convenient, quick service. If you are considering starting a hybrid salon, be sure to find a salon point-of-sale software that can help manage your business smoothly.